Untergrund: Warum grundieren? Welche Spachtelmasse passt? Welcher Klebstoff ist der richtige? Antworten auf diese Fragen geben wir hier.
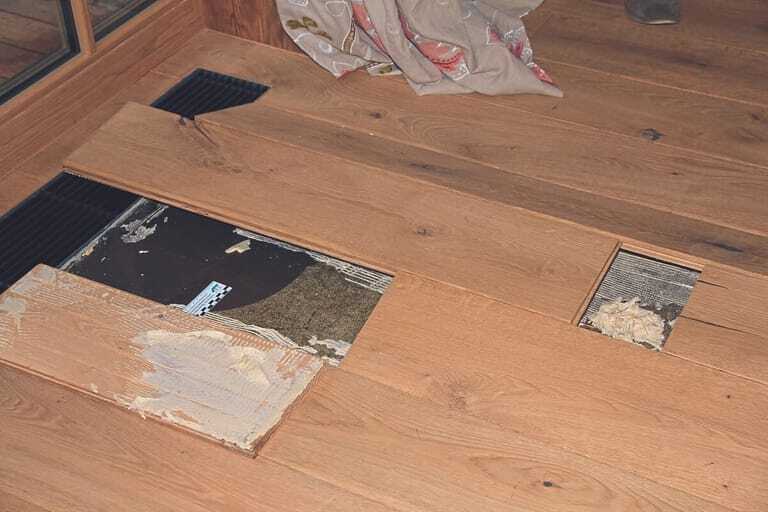
Ein komplettes System besteht immer aus drei Komponenten: Grundierung, Spachtelmasse und Klebstoff. Passt nur eines der drei Elemente nicht in den Systemaufbau, weil es zum Beispiel aus chemischer Sicht ungeeignet ist, führt das zu Problemen.
"Das Zusammenspiel der einzelnen Komponenten ist extrem komplex“, sagt Dr. rer. nat. Jörg Sieksmeier, Leiter Forschung und Entwicklung bei der Ardex GmbH, zu Beginn seines Vortrages zum Thema "Wirkungsweise von Grundierungen unter Spachtelmassen und Klebstoffen" beim 18. internationalen Sachverständigentreffen des Bundesverbandes Estrich und Belag (BEB).
Nur wer über Systemkompetenz verfügt, könne den Untergrund richtig beurteilen und vorbereiten, die passende Grundierung und Spachtelmasse sowie den geeigneten Klebstoff auswählen und auftragen. Erst im letzten Schritt folgt schließlich die Verlegung des Bodenbelags. Was alles schieflaufen kann, wenn die einzelnen Komponenten nicht richtig ausgewählt oder ausgeführt werden, musste Sieksmeier selbst miterleben.
Nach einem Wasserschaden in seinem Wohnzimmer sollte das 20 Jahre alte Parkett ausgetauscht werden. Das erste Problem: Der Untergrund wurde nicht bis zur tragfähigen Fläche gefräst. Fehler Nummer zwei: Die Handwerker verdünnten die Grundierung zu sehr. Schlussendlich wurde die Spachtelmasse nicht dick genug aufgetragen und der Kleber war nicht für die Anforderungen des Bucheparketts geeignet.
Das Ergebnis: Der neu verlegte Boden löste sich bereits nach kurzer Zeit ab, der Belag musste wieder komplett zurückgebaut und entfernt werden. Dieses Beispiel zeigt, dass sich der Handwerker nicht nur mit den Eigenschaften, sondern auch mit der Anwendung der einzelnen Komponenten auskennen sollte.
1. Die Grundierung
Eine Grundierung kann verschiedene Funktionen erfüllen. Welche in der konkreten Situation nötig sind, hängt von den Umgebungsbedingungen ab. "Die eierlegende Universal-Grundierung, die alles kann, gibt es nicht“, sagt Sieksmeier gleich vorneweg. Stattdessen muss der Handwerker die Umgebungsbedingungen überprüfen und in Abhängigkeit davon die richtige Grundierung auswählen.
Bei saugfähigen Untergründen ist es zum Beispiel wichtig, eine Grundierung zu wählen, die die Saugfähigkeit des Bodens reduziert. Dadurch wird verhindert, dass der Untergrund das Wasser der Spachtelmasse innerhalb kurzer Zeit aufsaugt und diese daraufhin "verdurstet". "Wenn eine Spachtelmasse nur 30 Prozent ihrer eigentlichen Hydratationsfähigkeit erhält, wird die anschließende Belagverlegung schiefgehen“, sagt Sieksmeier. Daher empfiehlt er, bei stark saugfähigen Untergründen eine wässerige Acrylatdispersion zu nutzen, die sowohl zum Untergrund als auch zur nachfolgenden Spachtelmasse beziehungsweise zum Klebstoff haftaktiv ist.
Die Saugfähigkeit des Untergrundes kann der Handwerker durch den Wassertest prüfen, die Tragfähigkeit des Untergrundes durch Witschtest und Kratzprobe.
Je nach Substrat, wie Estrich, Metall, Beschichtung oder Keramik, dient eine Grundierung aber auch dazu, eine Haftbrücke aufzubauen. Nachfolgende Tabelle 1 liefert eine Übersicht, welche Grundierung für welchen Untergrund geeignet ist.
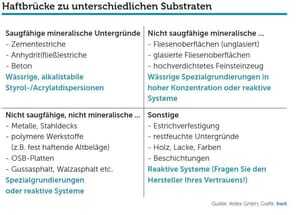
Dabei gilt, dass eine Grundierung immer nur so gut ist wie ihr Untergrund. "Bei einem Mischuntergrund kann die Grundierung in der Regel nicht mehr viel ausrichten“, sagt Sieksmeier. Diese stellen ein nicht kalkulierbares Risiko dar und sollten entfernt werden. Daneben rät er, auf wasserempfindlichen Untergründen keine wässrigen Grundierungen zu verwenden. Ist der Untergrund schwach gebunden, so sollte der Handwerker eine verfestigte Grundierung einsetzen.
Mit einer Grundierung ist es auch möglich, einen nicht ganz gelungenen Estrich zu verbessern, sodass dieser als Verlegeuntergrund dienen kann. Dafür bieten die Hersteller spezielle Produkte an. Staub wirkt generell als Trennmittel, da er einen Bindungsaufbau zu nachfolgenden Schichten und Klebstoffen verhindert. Schwachgebundene Zementestrichoberflächen müssen laut Sieksmeier ertüchtigt oder besser entfernt werden. Magnesiaestriche sollten mit einer Spezial-Grundierung geschützt werden, da diese sehr feuchteempfindlich sind. Bei porigen Untergründen muss die Grundierung einen Porenverschluss gewährleisten, denn diese Art von Untergründen führt zu einer Blasenbildung, sowohl in der nachfolgenden Spachtelung als auch in den Belagklebern.
Radonsperre in Deutschland noch nicht so populär
Daneben werden sogenannte funktionale Grundierungen in einer Vielzahl von Anwendungen eingesetzt, zum Beispiel als Wasserdampfdiffusionsbremse oder Radonsperre. "Wobei Letzteres bei uns in Deutschland noch nicht so populär ist“, sagt Sieksmeier.
Wird eine funktionale Grundierung auf restfeuchten Untergründen eingesetzt, empfiehlt Sieksmeier, die CM-Messung beziehungsweise zusätzlich die KRL-Methode anzuwenden. Insgesamt rät Sieksmeier, bei Grundierungen für Spezialanwendungen den Nachweis des Herstellers anzufordern.
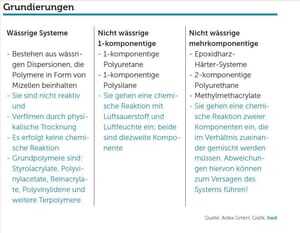
Wie Tabelle 2 zeigt, werden die am Markt verfügbaren Grundierungen grundsätzlich in drei Klassen einsortiert: wässrige Systeme, nicht wässrige 1-komponentige Systeme und nicht wässrige mehrkomponentige Systeme.
Wichtig ist laut Sieksmeier, dass die wässrigen Grundierungen im Gegensatz zu den funktionalen 1- und mehrkomponentigen Grundierungen nicht chemisch reagieren, sondern physikalisch verfilmen. Wie die Filmbildung bei wässrigen Dispersionsgrundierungen abläuft, stellt Grafik 1 in vereinfachter Weise dar.
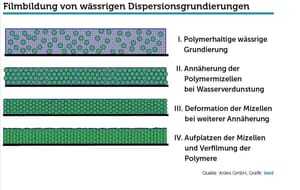
Dabei verfügt jede Dispersion über eine Mindestfilmbildungstemperatur, die sogenannte MFT, die in den Anwenderinformationen vermerkt ist. "Baugrundierungen sollten über eine MFT von mindestens fünf Grad Celcius verfügen“, sagt Sieksmeier. "Ansonsten müssen die raumklimatischen Bedingungen an die Dispersion angeglichen werden. Denn bei Unterschreitung der MFT bildet die Dispersion keinen geschlossenen Film aus.“
Die nicht wässrigen, 1-komponentigen Grundierungen sind keine Grundierungen im herkömmlichen Sinne, da sie meist nur zum Untergrund haftaktiv sind. Sie gehören vielmehr zur Gruppe der funktionalen Bindemittel und werden zum Beispiel als Wasserdampfsperre oder für die Sanierung von Untergründen eingesetzt.
Die Grundierungen benötigen auf der Baustelle einen Reaktionspartner, in diesem Fall Feuchtigkeit aus der Luft oder dem Untergrund. "Ist die relative Feuchtigkeit sehr gering, wie es zum Beispiel im Winter der Fall sein kann, muss der Handwerker für die entsprechende Feuchtigkeit sorgen“, sagt Sieksmeier. Da die Oberfläche der abreagierten 1-komponentigen Grundierung auf Polyurethan- oder SMP-Basis nicht ausreichend haftaktiv zur nachfolgenden Spachtelung ist, müssen sie, bevor die Spachtelung erfolgen kann, entsprechend abgesandet oder mit einer haftaktiven Grundierung versehen werden.
Die nicht wässrigen mehrkomponentigen Grundierungen sind ebenfalls keine Grundierungen im klassischen Sinn. Sie gehen mit dem Härter eine chemische Reaktion ein, die im richtigen Verhältnis zueinander gemischt werden muss. Abweichungen hiervon können zum Versagen des Systems führen. "Das gilt nicht nur für den Härterunterschuss, sondern auch für den Härterüberschuss“, sagt Sieksmeier.
2. Die Wasserdampfbremse
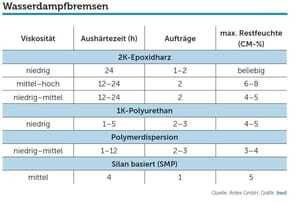
Für die erfolgreiche Verlegung des Bodenbelages ist es elementar, dass der Belag vor Feuchtigkeit geschützt wird. Verschiedene Normen und Merkblätter fordern hierfür empirisch ermittelte Feuchtigkeitsgrenzwerte für die unterschiedlichen Untergründe. "Fakt ist aber, dass die Untergründe meistens einen deutlich höheren Feuchtigkeitsgrad haben, als in den Merkblättern angegeben wird, und die Baustelle zusätzlich nächste Woche fertig sein muss“, sagt Sieksmeier.
Also kommen häufig sogenannte Wasserdampfbremsen oder -sperren zum Einsatz, wie 2-K-Epoxidharz, 1-K-Polyurethan, eine Polymerdispersion oder eine SMP-Dispersionsgrundierung. "Warum gibt es so viele?“, fragt Sieksmeier. "Weil es so viele unterschiedliche Feuchtigkeitsfälle gibt.“ Eine Übersicht, welche Wasserdampfbremse bei welcher Feuchtigkeit eingesetzt werden sollte, bietet Tabelle 3.
Folgende Situationen können dabei auftreten (Klebstoff und Spachtelmasse sind nicht feuchtestabil):- Die verwendete Feuchtesperre ist nahezu diffusionsdicht, die nachfolgenden Schichten werden nicht beschädigt.
- Die Feuchtigkeit, die aus dem Estrich dringt und durch die diffussionshindernde Grundierung, die Spachtelmasse und den Klebstoff bis hin zum Bodenbelag wandert, ist geringer als die Feuchtigkeit, die durch den Belag abgegeben werden kann. Kein Schaden. "Dies funktioniert aber nur, wenn zwischendurch keine speichernde Schicht eingebaut wurde, wie zum Beispiel eine Spachtelmasse“, sagt Sieksmeier.
- Es dringt deutlich mehr Feuchtigkeit durch die Wasserdampfbremse, als der Belag abgeben kann. "Klarer Fall: Es entsteht ein Schaden“, sagt Sieksmeier, "wie Beulen, Blasen oder Schimmelpilz.“
- Es dringt genauso viel Feuchtigkeit durch die Wasserdampfbremse hindurch, wie auch durch den Oberbelag abgegeben werden kann. "In diesen Fällen entsteht trotzdem zu 80 Prozent ein Schaden, da in der Regel eine Spachtelmasse als Speichermedium dazwischen liegt“, sagt Sieksmeier.
3. Der SD-Wert
Der Wasserdampfdiffusionswert, der sogenanntem sd-Wert, ergibt sich aus der Multiplikation von Wasserdampfdiffusionswiderstandszahl (m) und der Schichtdicke der Membran (d). Er gibt an, wie dick eine Luftschicht sein müsste, um die gleiche Dichtigkeit wie ein Grundierungsfilm oder eine Abdichtungsschicht bei der applizierten Dicke zu erreichen. Kurz gesagt: Je höher der Wert, desto weniger Feuchtigkeit diffundiert durch das Material.
Bei einem sd-Wert bis 0,5 Metern gilt die Grundierung als "wasserdampfdiffusionsoffen“, bei einem Wert von 0,5 bis 1.500 Metern als "hemmend“ (Wasserdampfbremse) und bei einem sd-Wert ab 1.500 Metern spricht man von der sogenannten "Wasserdampfdiffusionsdichtigkeit“ ( Wasserdampfsperre), das Material ist also vollkommen dicht, vergleichbar mit einer Alufolie.
Wie in Tabelle 4 zu sehen ist, sind die Messmethoden des sd-Wertes jedoch unterschiedlich und nicht immer miteinander vergleichbar.
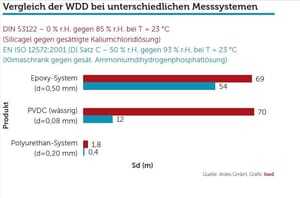
Hinzu kommt, dass der m-Wert, aus dem sich der spätere sd-Wert zusammensetzt, laut Sieksmeier genauso fehlerhaft zu messen ist wie der eigentliche Endwert. "Das erklärt auch, warum 2-komponentige Polyurethan-Wasserdampfbremsen, die über einen niedrigen sd-Wert von zum Beispiel 1,8 Metern verfügen und damit eigentlich zu einem Schaden führen müssten, in der Realität trotzdem sehr gut funktionieren“, sagt Sieksmeier.
4. Die Spachtelmasse
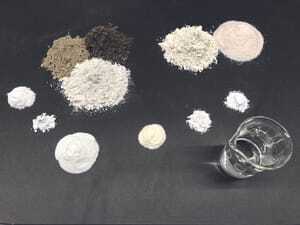
Nach der Grundierung folgt die Spachtelmasse, ein ebenfalls wichtiger Bestandteil des Systems. Ihre Aufgabe ist es, durch Höhenausgleich einen ebenen Untergrund zur Aufnahme von Bodenbelägen oder zur direkten Nutzung zu schaffen sowie den Haftgrund f ür den Klebstoff zu bilden.
Dabei bestehen die heute am Markt verfügbaren Spachtelmassen – wie viele annehmen – nicht mehr nur aus Sand und Zement (siehe Bild). Im Gegenteil: "Heutige Spachtelmassen sind hochkomplexe Systeme mit zahlreichen Bestandteilen“, sagt Sieksmeier.
Prinzipiell unterscheidet er zwischen vier Arten:- Zementgebundene Spachtelmassen: SZ-B (binäre Systeme mit schneller Erhärtung, aber verzögerter Trocknung), SZ-T (ternäre Systeme mit schneller Erhärtung und schneller Trocknung).
- Gipsgebundene Spachtelmassen: auch als Alpha-Halbhydrat, Anhydrit oder Calciumsulfat bezeichnet.
- Dispersionsspachtelmassen.
- Reaktionsharzspachtelmassen: zum Beispiel PUR, EP, PES, PMMA.
5. Der Klebstoff
Nach der Spachtelmasse folgt der Klebstoff. Auch hier gibt es unterschiedliche Klassen, dazu gehören:- Dispersionsklebstoff: Die wasserbasierten Nass- beziehungsweise Haftklebstoffe bestehen zu circa 35 Prozent aus Dispersion und zu circa 40 Prozent aus Füllstoffen. Durch physikalisches Verdunsten von Wasser erfolgen die Verfilmung der Harz- und Dispersionsteilchen und damit der Festigkeitsaufbau des Klebstoffes.
- Reaktionsharzklebstoff: Die Klebstoffe bestehen je nach Rohstoffbasis aus ein oder zwei Komponenten. Zu dieser Gruppe gehören 1-K PUR, 1-K Hybrid/MS, 2-K PUR und 2-K EP. Erst durch die chemische Reaktion zweier Reaktionspartner entsteht ein fester Klebeverbund.
- Kunstharzklebstoff: Bestehen zu circa 14 Prozent aus Kunstharz und zu circa 22 Prozent aus Lösemitteln. Durch physikalisches Verdunsten der Lösemittel erfolgen die Verfilmung der Harzteilchen und damit der Festigkeitsaufbau des Klebstoffes.
- Neoprenklebstoff: Bestehen zu circa 73 Prozent aus Lösemitteln. Die Verfilmung der Kunstkautschukteilchen erfolgt durch physikalisches Verdunsten der Lösemittel. Der Festigkeitsaufbau des Klebstoffes wird durch hohen Pressdruck erreicht.
- Hybridklebstoff: Diese elastomeren Klebstoffe weisen einen geringen Vernetzungsgrad auf, "sind nicht mehr lösemittelhaltig und funktionieren trotzdem“, sagt Sieksmeier.
6. Die Umweltsiegel
Inzwischen gibt es zahlreiche Umweltsiegel auf dem Markt. In Deutschland relevant sind vor allem Emicode EC1 Plus, Emicode EC1, der Blaue Engel und die AgBB/DIBt. Jedes Institut hat dabei andere Vergabekriterien. Welches Siegel die höchsten Anforderungen stellt und damit die höchste Sicherheit bietet, zeigt Tabelle 5.